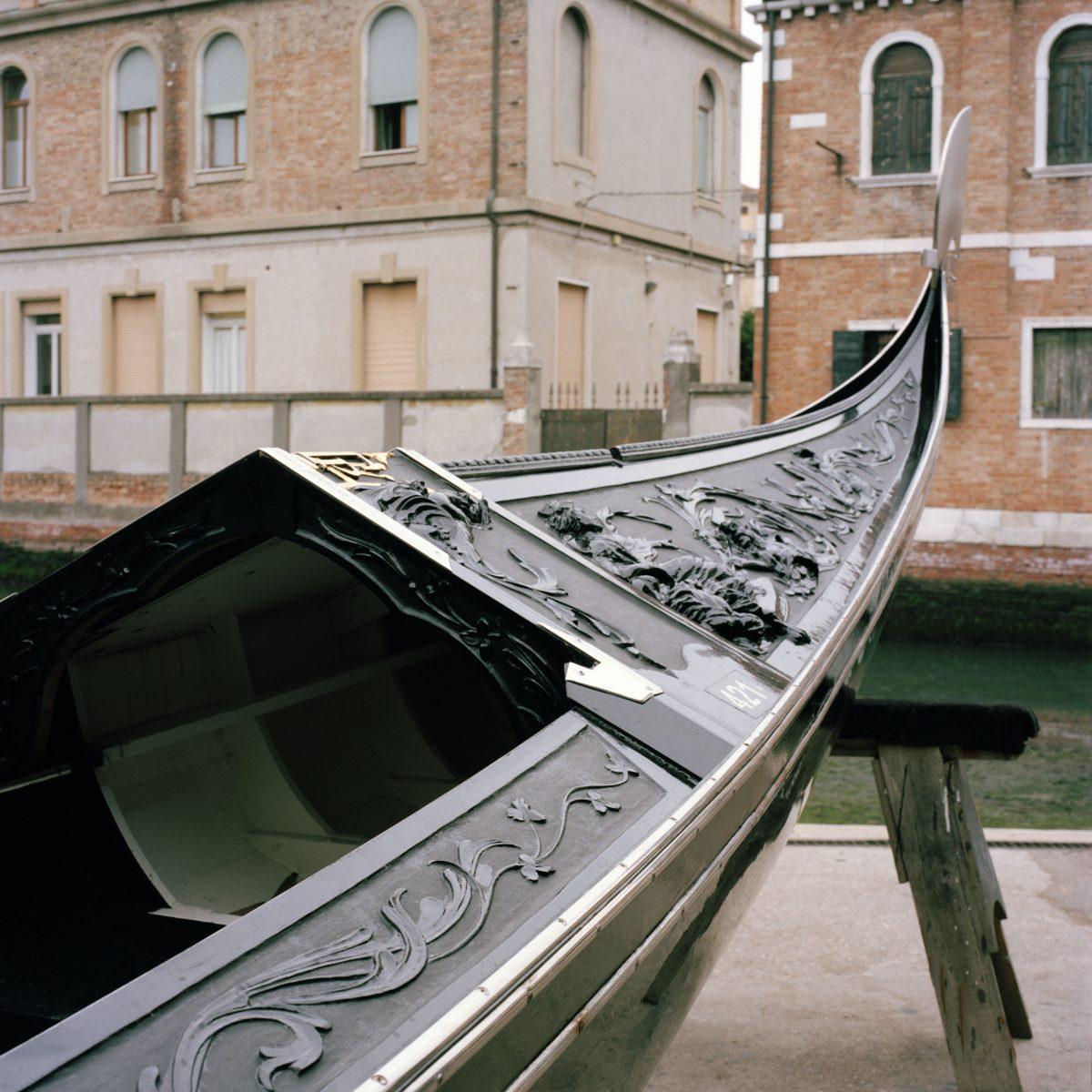
Before 1884, gondolas were symmetrical, and two gondoliers had to row the boat by standing on opposite sides of the hull. Tramontin designed an asymmetrical hull, causing the gondola to become imbalanced in such a way that it created a natural bias on one side. This weight imbalance meant that a single gondolier could row on one side and maintain a straight line. Many boatyards copied Tramontin’s new, innovative design.
Constructing a Tramontin Gondola
Every Tramontin gondola is custom-made. The weight of the stern, where the gondolier stands, depends on the weight of the gondolier: The heavier the boatman, the higher the stern needs to sit in the water to compensate.The gondolier can also request specifics, such as the carvings and the type of “ferro” (the distinctive metal ornament at the front of the gondola). The six “teeth” on a traditional Venetian ferro are thought to represent the six districts of Venice.
Building a custom gondola takes five months. The first two months are purely for construction. At the workshop, workers use the same boat-length wooden beam with its metal markers that Tramontin’s ancestors used in 1884 to act as a guide for constructing the boats’ bellies with their characteristic wooden ribs.
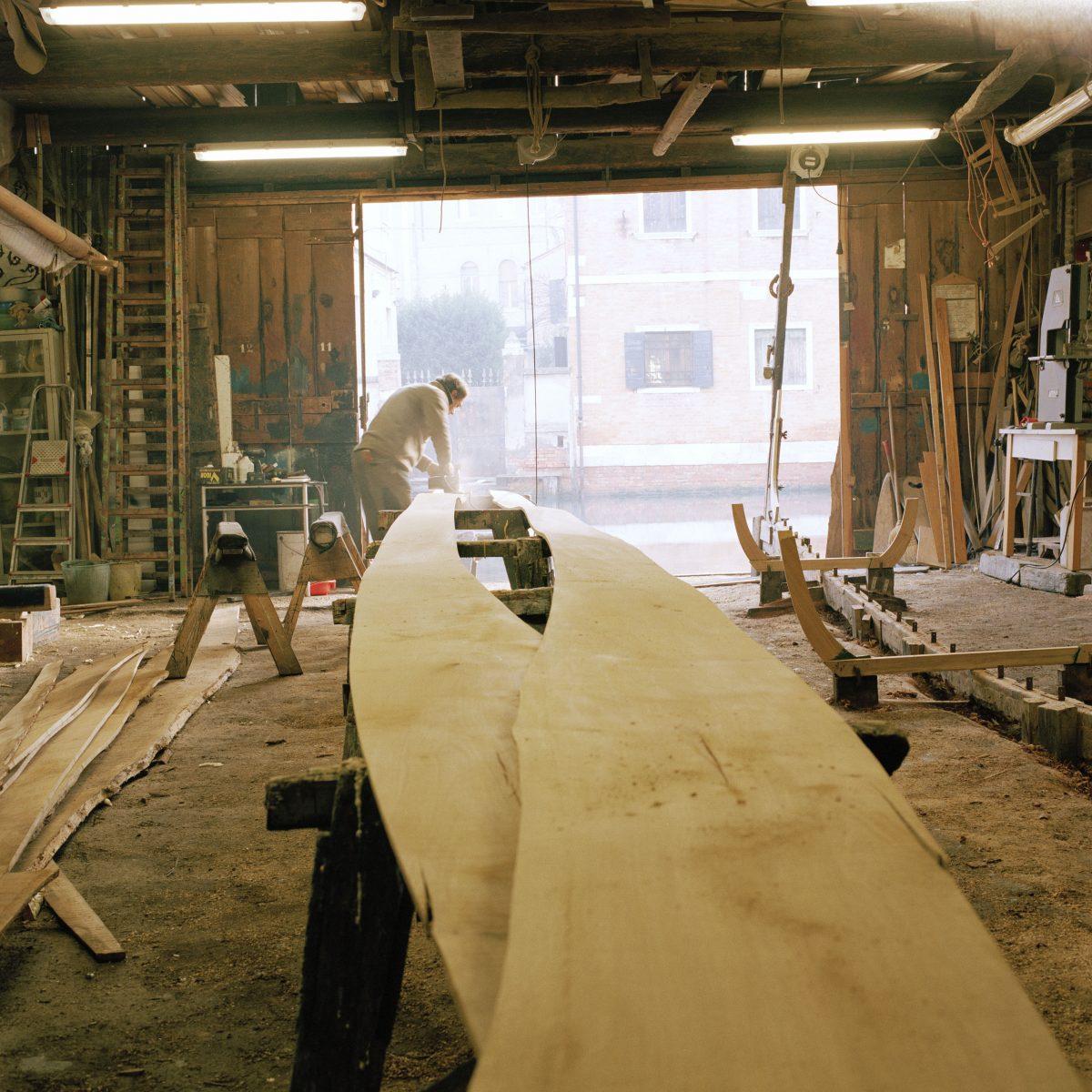
Eight types of wood are used throughout the gondola, each performing a different function based on their natural strengths: Oak’s solidity is used for the sides; fir is lightweight enough for use on the boat’s bottom; cherry is easy to shape and is used for the thwarts, or struts, that span the inside of the gondola; walnut and elm are flexible enough to be used for the frame; linden is stable; mahogany is used for its structural integrity; and lastly, larch, being both lightweight and solid, provides the gondola with good water resistance.
Before shaping the wood, in order to avoid damaging the wood fibers, each piece is first soaked in water and then heated over fire. For most of the gondola’s construction, the workers use simple hand tools: an ax, plane saw, and hammer.
The master woodcarver then decorates the top panels of the gondola, which takes two months. The gondolier’s initials and the boatyard’s mark can be found on the stern, carved into a piece of wood called a “catenella.”
The final month of the five is spent painting the gondola with six coats of glossy black paint. The striking black paint is a tradition that was set back in 1562 when the Venetian authorities decreed that black paint must be applied to all but ceremonial gondolas. The order was to end the competitive mentality of the gondoliers, who increasingly sought more and more elaborate decoration for their gondolas. In the gondola’s heyday, around 10,000 of these vessels were on the waterways of Venice; now they number a few hundred.