Meet Mariano Palencia Crespo of MPC Bespoke, one of London’s bespoke bootmakers.
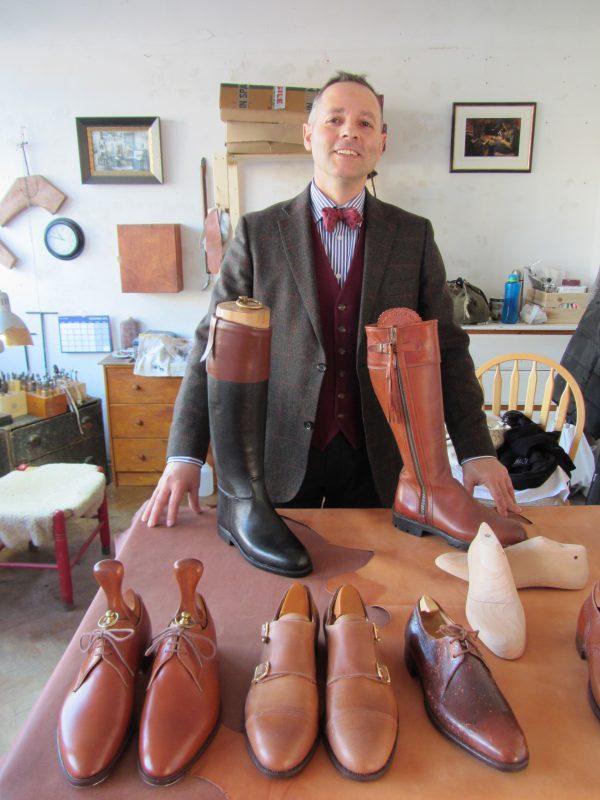
Bespoke bootmaker Mariano Palencia Crespo in his workshop with a selection of his handcrafted boots and shoes made from vegetable-tanned leather from European hides. Courtesy of Mariano Palencia Crespo