Commentary
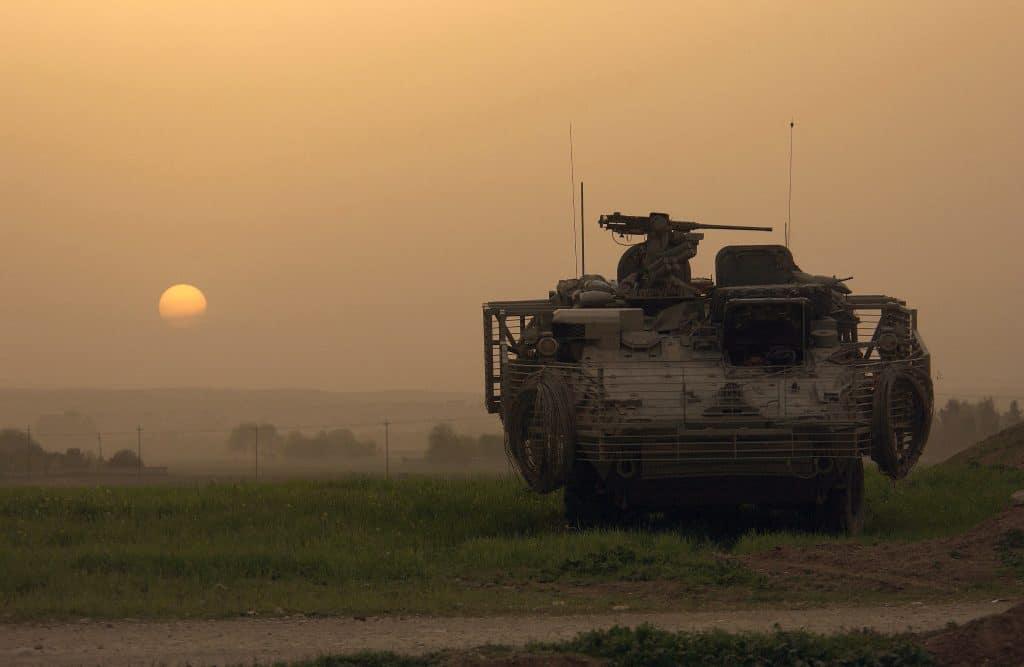
A U.S. Army M1126 Stryker Infantry Carrier Vehicle, from 2nd Platoon, Bravo Company, 1st Battalion, 5th Infantry, 25th Infantry Division (Stryker Brigade Combat Team), fitted with Slat Armor cage, conducts a patrol near Mosul, Iraq, as the sun sets, on March 31, 2005. DoD
Stephen B. Lewis has been an educator and an athletic coach for nearly 30 years. For much of that time, he was a successful high school and college football coach in Connecticut. After the events of 9/11, many of Steve’s former athletes joined the military. In the succeeding years, they didn’t return the same way they went out, and this led Steve to become interested in veteran affairs. In 2017 he conducted the first annual Comfort Walk, a 70-mile three-day trek from Manchester, Connecticut, to Providence, Rhode Island, on Memorial Day weekend to raise awareness of veterans’ mental health issues. In 2017 Steve also assisted the veterans of the 1-24th Infantry Regiment in their Walk of Life. Steve regularly participates in the Connecticut Run for the Fallen and has helped out in other veteran events and presentations, including hosting a veteran’s assembly and classroom visit to his school. A civilian, Steve comes from a military family as the son of a U.S. Military Academy West Point 1952 graduate and grandson of a November 1918 graduate. He has previously authored articles on fisheries issues and is looking forward to contributing his writing talents to military matters and veterans' advocacy.
Author’s Selected Articles